In the fast-paced world of manufacturing, the demand for improved efficiency and reduced operational costs has never been greater. As industries evolve, so too do the tools and technologies required to meet these challenges. Among the most significant innovations in welding technology is the emergence of high-efficiency all-in-one welding systems. These cutting-edge devices are designed to streamline the welding process while enhancing performance, productivity, and versatility. In this article, we will explore the key features, benefits, and applications of these advanced systems, as well as their impact on the welding landscape.
Understanding High-Efficiency All-in-One Welding Systems
High-efficiency all-in-one welding systems represent a revolutionary shift in MIG (Metal Inert Gas), TIG (Tungsten Inert Gas), and stick welding processes. These systems combine multiple welding functions and capabilities into a single, compact unit. Traditional welding setups often involve multiple machines for different welding methods, which can lead to logistical challenges, inefficiencies, and increased costs. In contrast, an all-in-one system eliminates the need for separate equipment, allowing operators to switch between different welding processes seamlessly.
Key Features
1. **Versatility**: One of the most notable features of high-efficiency all-in-one welding systems is their versatility. With the ability to handle various welding processes—MIG, TIG, and stick welding—these machines can cater to a diverse range of applications, from automotive repair to heavy industrial fabrication.
2. **Compact Design**: Many all-in-one systems are designed with space-saving in mind. The integration of multiple functions into a single, compact unit allows for more efficient use of workshop space, making them ideal for smaller facilities or mobile applications.
3. **User-Friendly Interface**: Advanced welding systems often come equipped with intuitive digital displays and user-friendly controls. This technology simplifies the setup and operation process, allowing even less experienced operators to achieve high-quality welds.
4. **Energy Efficiency**: With efficient design and power management features, these systems consume less electricity, reducing operational costs and contributing to a smaller environmental footprint.
5. **Enhanced Functionality**: Modern all-in-one welding systems often include additional features such as automatic voltage adjustment, spool gun compatibility, and advanced cooling systems. These enhancements not only improve performance but also extend the machine’s life.
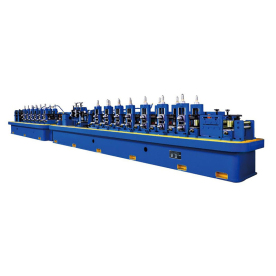
Enhancing Performance and Productivity: An In-Depth Look at High-Efficiency All-in-One Welding Systems for Modern Manufacturing
Benefits of High-Efficiency All-in-One Welding Systems
1. **Cost Savings**: The initial investment in a high-efficiency all-in-one welding system can be offset by the savings from reduced equipment costs and maintenance. Fewer machines mean lower overhead costs for businesses, as well as potential savings on energy consumption.
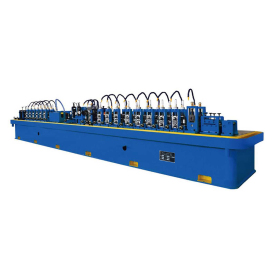
Enhancing Performance and Productivity: An In-Depth Look at High-Efficiency All-in-One Welding Systems for Modern Manufacturing
2. **Improved Productivity**: The ability to switch between different welding processes without the need to change machines can significantly reduce downtime. This means that projects can be completed faster without compromising the quality of the welds.
3. **Higher Quality Welds**: Advanced technology and features embedded in these systems contribute to improved precision and consistency in welding operations. This is particularly important in industries that prioritize quality control, such as aerospace and automotive manufacturing.
4. **Simplified Training**: With a single machine that can perform multiple welding functions, training employees becomes more straightforward. Operators can learn one system instead of needing to be proficient with multiple machines, thereby speeding up the onboarding process.
5. **Greater Innovation Opportunities**: Because these systems are often equipped with the latest technology, they provide manufacturers with the tools needed to innovate. Enhanced capabilities allow for exploring new techniques and applications, keeping businesses competitive in a rapidly evolving market.
Applications Across Industries
The high-efficiency all-in-one welding system is suitable for various industries, including:
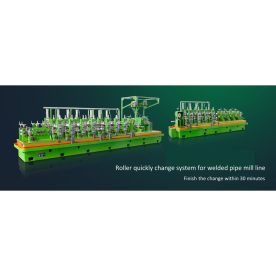
Enhancing Performance and Productivity: An In-Depth Look at High-Efficiency All-in-One Welding Systems for Modern Manufacturing
– **Automotive Manufacturing**: Welding is critical for the production of vehicle frames and components. All-in-one systems can provide the flexibility needed for different materials and welding processes. – **Construction and Fabrication**: These machines can handle the diverse welding requirements often encountered on construction sites, from structural work to metal fabrication.
– **Maintenance and Repair**: For repair shops, having a versatile welding system simplifies repair processes, allowing technicians to address a wide range of welding tasks with a single machine.
– **Artistic Applications**: Artists and metalworkers can take advantage of these systems to explore creative welding applications, ranging from sculptures to custom furniture.
Conclusion
High-efficiency all-in-one welding systems are quickly becoming essential tools in modern manufacturing. Their combination of versatility, cost-effectiveness, and advanced technology makes them invaluable for businesses striving to enhance productivity and quality. As industries continue to evolve, investing in these systems not only prepares companies to meet current demands but also equips them for future challenges. By embracing these innovations, manufacturers can stay ahead of the curve and ensure their long-term success in a competitive marketplace.Precision ERW tube mill machinery